Vedanta Aluminium, Runaya Refining win ‘Gold’ for green technology partnership
Vedanta Aluminium produces more than half of India’s aluminium at 1.97 million metric tonnes, at its smelters in Jharsuguda (Odisha) and BALCO (Chhattisgarh)
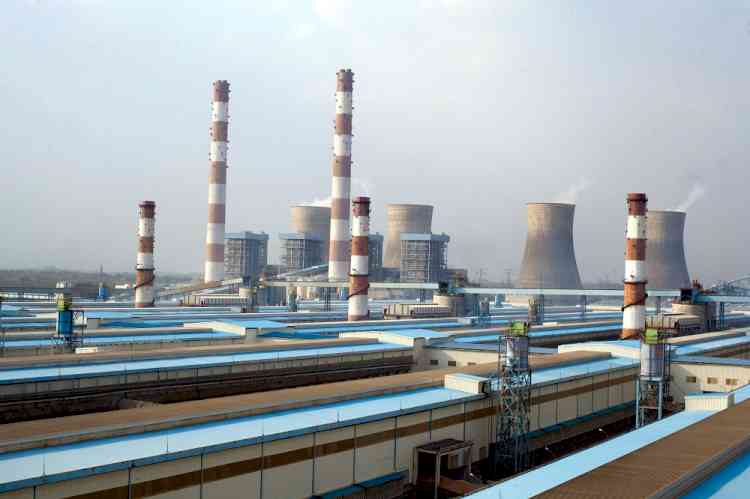
Chandigarh, January 20, 2022: Vedanta Aluminium Business, India’s largest producer of aluminium and value-added products and Runaya Refining, one of India’s fastest growing manufacturing start-ups, have won the ‘Gold’ award at the (Business World) BW Recycling for a Greener Tomorrow Awards 2022 in ‘Best in Recycling or Material Recovery Facility of the Year’ category.
Vedanta Aluminium produces more than half of India’s aluminium at 1.97 million metric tonnes, at its smelters in Jharsuguda (Odisha) and BALCO (Chhattisgarh). Approximately 1.5% of the total quantity is lost in the form of aluminium dross, a by-product that contains recoverable aluminium, aluminium nitrides and oxides, spinel, dimagnesium silicate, gupeiite, and sodium titanate. Runaya Refining, through a technological tie-up with TAHA International S.A., is not only able to improve aluminium recovery to nearly 90%, but also creates value-added products for other industries. After recovering aluminium, Runaya takes the non-metallic portions of the residual dross and processes it to produce briquettes which are used as slag conditioner in the steel industry. At Vedanta’s facility in Jharsuguda, using Runaya’s dross technology has not only ensured a significantly higher metal recovery rate, but also created energy savings to the tune of 800,000 GJ and reducing CO2 emissions in excess of 260,000 tonnes, annually.
Rahul Sharma, CEO – Aluminium Business, Vedanta Limited said, “Our partnership with Runaya to eliminate waste and recover metal through a patented cutting-edge technology is such an example.”
Annanya Agarwal, CEO – Runaya Refining, added, “Through this pioneering partnership, Vedanta Aluminium and Runaya Refining are not just eliminating an entire waste stream, but also decreasing the steel industry’s dependence on virgin raw materials for slag conditioners – thereby living up to the ideals of circular manufacturing and circular economy.”